Τhe efficient solution for high pressures
HYGHSPIN DOUBLE FLOW
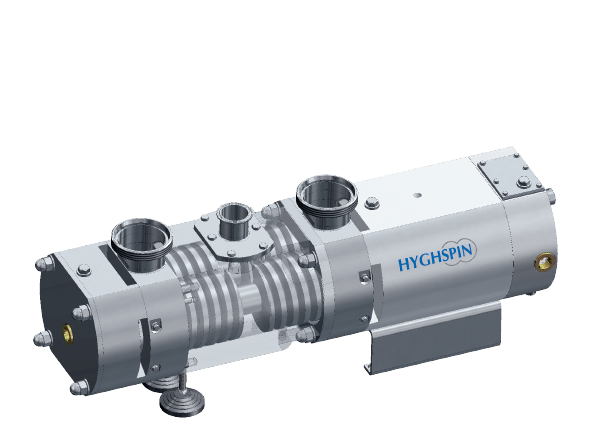
Twin-screw pumps from the HYGHSPIN series are the perfect solutions for countless applications
Innovative and hygienic design, highly economical, optimum MTTR value – main reasons for HYGHSPIN.
The HYGHSPIN stainless steel pump series from Jung Process Systems have been proved worldwide and can be used for flowable products with practically all viscosities and consistencies – whether aqueous, highly viscous, lumpy, fibrous, or gas-laden.
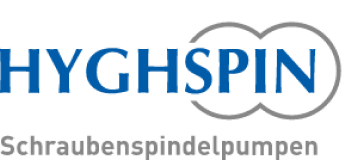
HYGHSPIN Double Flow twin-screw pump – the efficient solution for high pressures
Double-flow, hygienic, high performance
The HYGHSPIN Double Flow extends the application range of the HYGHSPIN series, with high pressure differences up to 50 bar. This permits the HYGHSPIN advantages to be used also in high-pressure applications.
The HYGHSPIN Double Flow is a double-flow stainless steel twin-screw pump. It is fitted with two external inlet connections and one central outlet connection. Bearings on both ends keep shaft deflection under control. The high pressures due to axial thrust are compensated internally. Shaft seals are arranged on the suction side. In spite of the high pressure differences, all the main components are not subjected to high loads, which results in high reliability and outstanding service life. Moreover, the parallel use of two stages opens up the possibility for high volume flows.
The HYGHSPIN Double Flow is the hygienic and gentle solution for high-pressure applications.
Optionally, it comes in the sizes of 90, 105 and 125. Max. pumping volume is about 100 m³/h. Pressure difference is up to 50 bar.
HYGHSPIN Double Flow - Non contact and hygienic for high pressures
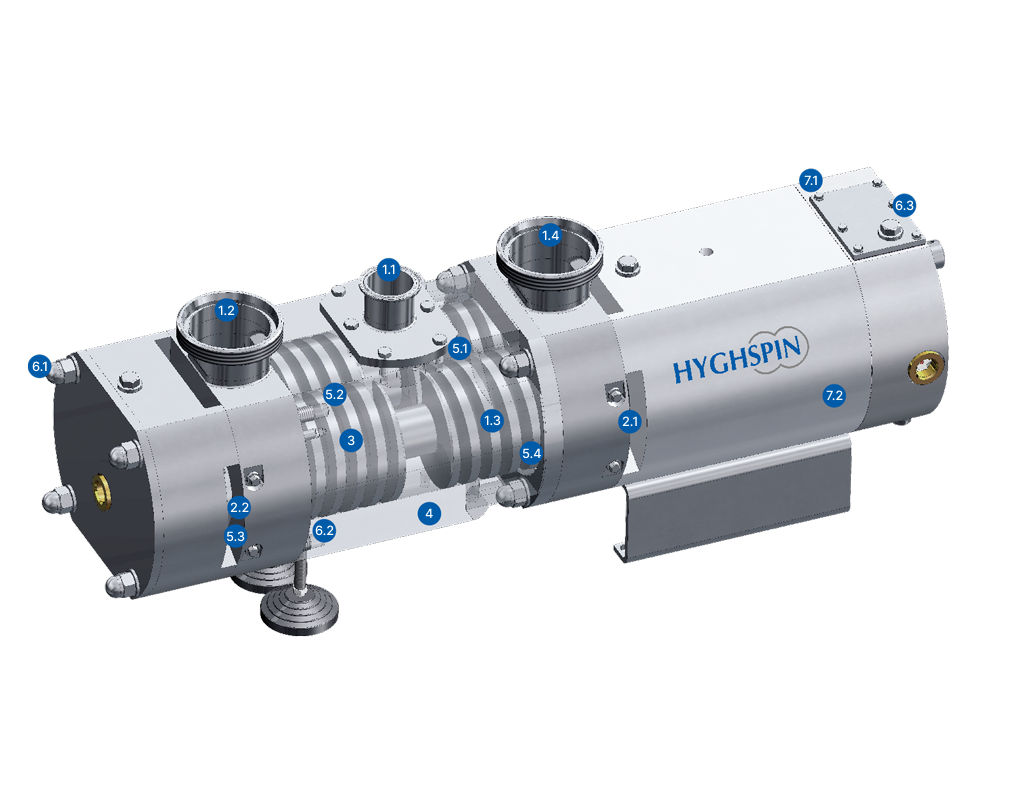
-
1. Modular system
1.1 Pump outlet
- Various nominal diameters and standards available, installation face-down is optional
1.2 Pump inlet
- Various nominal diameters and standards available, installation face-down is optional
1.3 Conveying element
- Various exchangeable conveying elements in one design size
1.4 Pump inlet
- Various nominal diameters and standards available
-
2. Shaft seal
2.1 Same installation space for:
- Simple-acting slip-ring seal
- Double-acting slip-ring seal (safe-to-run dry with rinsing)
- Lip seal in cartridge design (safe-to-run dry without rinsing)
2.2 Same installation space for:
- Simple-acting slip-ring seal
- Double-acting slip-ring seal (safe-to-run dry with rinsing)
- Lip seal in cartridge design (safe-to-run dry without rinsing)
-
3. Conveying element
- Smooth tracking conveying elements
- Revolution regulating from 5 up to 130 Hz
- Product conveying and cleaning with just one pump
- Very good suction capacity and low NPSH values
- Axial, gentle to products conveying
- Conveying for lumpy goods
- Conveying for gas charged media
- Optional: kolsterised finish surface
-
4. Pump housing
- Wear resistant Jung chrome carbide coating
- Optional: kolsterised finished surfaces
-
5. Hygienic design
5.1 Cleaning
- Ideal cleaning for the shaft seals as these are positioned in the cleaning flow
5.2 Finished surface for parts coming into contact with product
- Electropolished for an ideal cleaning (Ra <0,8)
- Optional: Ra <0,4
5.3 Cleaning
- Ideal cleaning for the shaft seals as these are positioned in the cleaning flow
5.4 Static seals
- Hygienic ring-shaped seal – no cavities
- FDA-approved elastometers in various qualities
-
6. Easy to service design
6.1 Four guide bolts with capped nuts
- Quicker assembly/dismantling for inspection, servicing and/or manual cleaning
- Guide bolts for damage-free handling of the components
6.2 Positioning
- Accurate positioning of the components due to precise production
6.3 Synchronisation gear wheels
- Inspection opening with access to the gearbox
- Setting the flank clearance in the system is possible without draining off the gearbox oil
-
7. Corrosion free pump
7.1 Gearbox housing
- Aluminium design with a wear resistant and acid resistant Teflon coating
- Optional: Stainless steel design
7.2 Bearing bracket
- Design in stainless steel with high-performance bearing
-
1. Modular system
1.1 Pump outlet
- Various nominal diameters and standards available, installation face-down is optional
1.2 Pump inlet
- Various nominal diameters and standards available, installation face-down is optional
1.3 Conveying element
- Various exchangeable conveying elements in one design size
1.4 Pump inlet
- Various nominal diameters and standards available
-
3. Conveying element
- Smooth tracking conveying elements
- Revolution regulating from 5 up to 130 Hz
- Product conveying and cleaning with just one pump
- Very good suction capacity and low NPSH values
- Axial, gentle to products conveying
- Conveying for lumpy goods
- Conveying for gas charged media
- Optional: kolsterised finish surface
-
5. Hygienic design
5.1 Cleaning
- Ideal cleaning for the shaft seals as these are positioned in the cleaning flow
5.2 Finished surface for parts coming into contact with product
- Electropolished for an ideal cleaning (Ra <0,8)
- Optional: Ra <0,4
5.3 Cleaning
- Ideal cleaning for the shaft seals as these are positioned in the cleaning flow
5.4 Static seals
- Hygienic ring-shaped seal – no cavities
- FDA-approved elastometers in various qualities
-
7. Corrosion free pump
7.1 Gearbox housing
- Aluminium design with a wear resistant and acid resistant Teflon coating
- Optional: Stainless steel design
7.2 Bearing bracket
- Design in stainless steel with high-performance bearing
-
2. Shaft seal
2.1 Same installation space for:
- Simple-acting slip-ring seal
- Double-acting slip-ring seal (safe-to-run dry with rinsing)
- Lip seal in cartridge design (safe-to-run dry without rinsing)
2.2 Same installation space for:
- Simple-acting slip-ring seal
- Double-acting slip-ring seal (safe-to-run dry with rinsing)
- Lip seal in cartridge design (safe-to-run dry without rinsing)
-
4. Pump housing
- Wear resistant Jung chrome carbide coating
- Optional: kolsterised finished surfaces
-
6. Easy to service design
6.1 Four guide bolts with capped nuts
- Quicker assembly/dismantling for inspection, servicing and/or manual cleaning
- Guide bolts for damage-free handling of the components
6.2 Positioning
- Accurate positioning of the components due to precise production
6.3 Synchronisation gear wheels
- Inspection opening with access to the gearbox
- Setting the flank clearance in the system is possible without draining off the gearbox oil
-
Advantages at a glance
- Pressure differences up to 50 bar
Shaft deflection is controlled by bearings on both ends - Wide range of volume flows
Two stages work in parallel, thereby permitting high volume flows - Long service life for bearings and shaft seals
Axial forces are compensated internally, and shaft seals are fitted on the suction side
Moreover, all the other advantages of HYGHSPIN twin-screw pumps apply
- Considerable cost savings
Reduced investment and maintenance costs - Best quality
Made completely of stainless steel - Exceptional service-friendliness
The pump must not be removed from the plant for maintenance work - Utmost flexibility
A wide range of products, viscosities, and quantities can be handled with a single pump - Pumping is gentle and smooth
Low speed, minimum pulsation, no pressure surges - Highest hygiene level
No dead spaces, and particularly good flushing of the shaft seal - CIP and SIP:
Cleaning and sterilisation within the plant, use as CIP feed pump
- Pressure differences up to 50 bar
-
Technical data/Performance features
Downloads
Let's stay in touch!
Contact us