Τhe most efficient solution for flowable products
HYGHSPIN
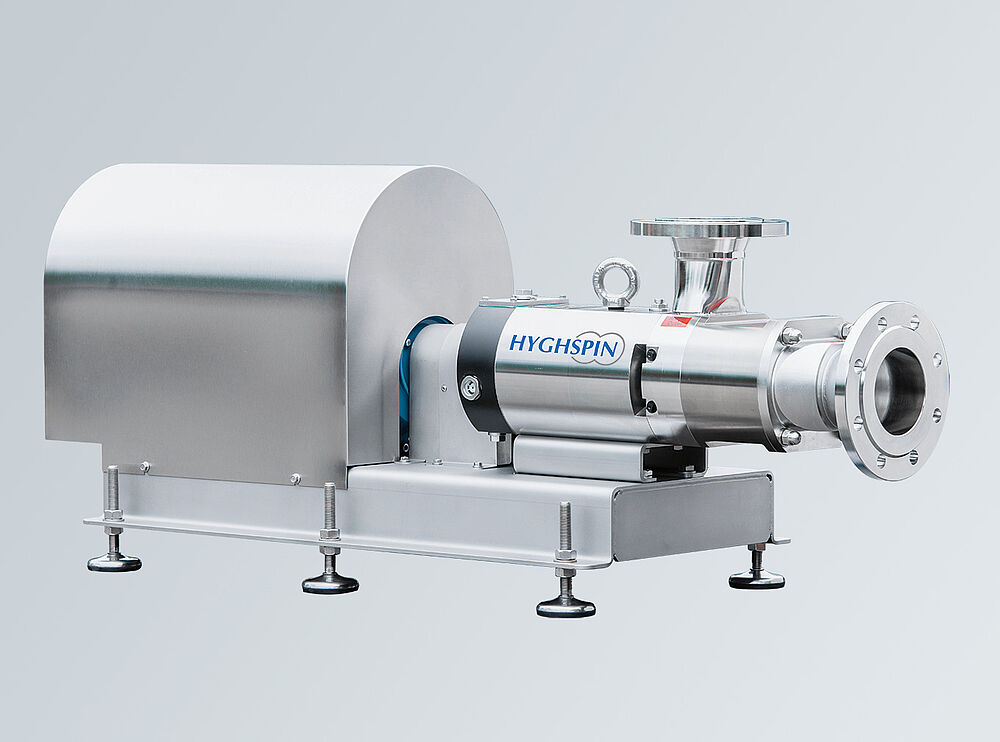
Twin-screw pumps from the HYGHSPIN series are the perfect solutions for countless applications
Innovative and hygienic design, highly economical, optimum MTTR value – main reasons for HYGHSPIN.
The HYGHSPIN stainless steel pump series from Jung Process Systems have been proved worldwide and can be used for flowable products with practically all viscosities and consistencies – whether aqueous, highly viscous, lumpy, fibrous, or gas-laden.
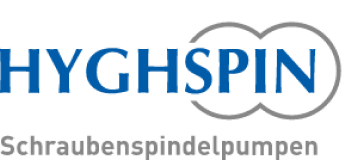
Twin-screw HYGHSPIN pumps – the most efficient solution for flowable products
Gentle product handling plus CIP with just one pump
The HYGHSPIN is the basic version of the worldwide proven HYGHSPIN pump series made of high-grade stainless steel. Whether aqueous, highly viscous, lumpy, fibrous, or gas-laden – the HYGHSPIN is suitable for flowable products of practically any consistency, and features utmost efficiency. These extremely service-friendly twin-screw pumps convince with a very high suction capacity, and gently transports all flowable products in quantities up to 300 m3/h. An additional pump for CIP cleaning is not necessary. This ensures considerable time and cost savings, thanks to lower outlay for investment and maintenance.
The HYGHSPIN stands for utmost flexibility, and is available in modular design or with a free shaft end.
It is available in sizes of 50, 70, 90, 105 and 125. Max. pumping volume is about 300 m³/h. Pumping pressure is up to 35 bar.
HYGHSPIN – Flexible applications – maximum efficiency
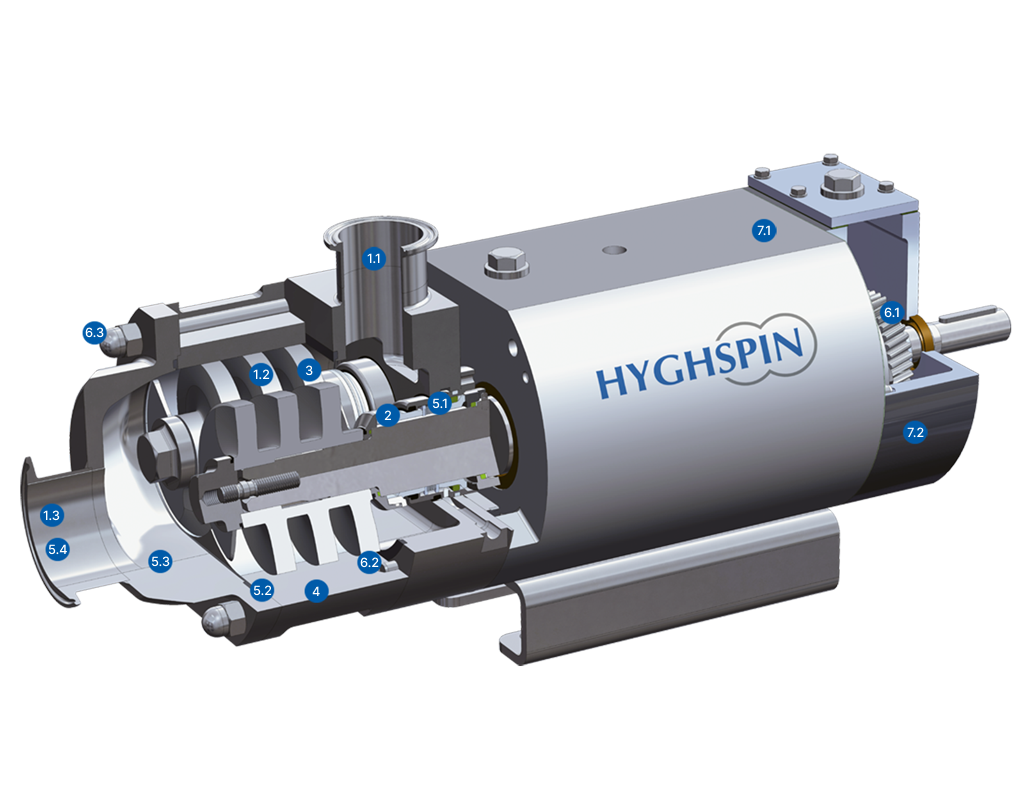
-
1. Modular system
1.1 Pump outlet/Pump inlet
- Reversible conveying is possible
- Various nominal diameters and standards available
- Various equipment top/bottom lateral or axial
1.2 Conveying element
- Various exchangeable conveying elements in one design size
1.3 Pump outlet/Pump inlet
- Reversible conveying is possible
- Various nominal diameters and standards available
-
2. Shaft seal
Same installation space for:
- Simple-acting slip-ring seal
- Double-acting slip-ring seal (safe-to-run dry with rinsing)
- Lip seal in cartridge design (safe-to-run dry without rinsing)
-
3. Conveying element
- Smooth tracking conveying elements
- Revolution regulating from 5 up to 130 Hz
- Product conveying and cleaning with just one pump
- Very good suction capacity and low NPSH values
- Axial, gentle to products conveying
- Conveying for lumpy goods
- Conveying for gas charged media
- Optional: kolsterised finish surface
-
4. Pump housing
- Wear resistant Jung chrome carbide coating
- Optional: kolsterised finished surfaces
- Optional: Heating jacket
-
5. Hygienic design
5.1 Cleaning
- Ideal cleaning for the shaft seals as these are fully integrated in the cleaning flow
5.2 Static seals
- Hygienic ring-shaped seal – no cavities
- FDA-approved elastometers in various qualities
5.3 Finished surface for parts coming into contact with product
- Electropolished for an ideal cleaning (Ra <0,8)
- Optional: Ra <0,4
5.4 Pump outlet/pump inlet
- Horizontal outlet for comprehensive draining
-
6. Easy to service design
6.1 Synchronisation gear wheels
- Inspection opening with access to the gearbox
- Setting the flank clearance in the system is possible without draining off the gearbox oil
6.2 Positioning
- Accurate positioning of the components due to precise production
6.3 Four guide bolts with capped nuts
- Quicker assembly/dismantling for inspection, servicing and/or manual cleaning
- Guide bolts for damage-free handling of the components
-
7. Corrosion free pump
7.1 Bearing bracket
- Design in stainless steel with high-performance bearing
7.2 Gearbox housing
- Aluminium design with a wear resistant and acid resistant Teflon coating
- Optional: Stainless steel design
-
1. Modular system
1.1 Pump outlet/Pump inlet
- Reversible conveying is possible
- Various nominal diameters and standards available
- Various equipment top/bottom lateral or axial
1.2 Conveying element
- Various exchangeable conveying elements in one design size
1.3 Pump outlet/Pump inlet
- Reversible conveying is possible
- Various nominal diameters and standards available
-
3. Conveying element
- Smooth tracking conveying elements
- Revolution regulating from 5 up to 130 Hz
- Product conveying and cleaning with just one pump
- Very good suction capacity and low NPSH values
- Axial, gentle to products conveying
- Conveying for lumpy goods
- Conveying for gas charged media
- Optional: kolsterised finish surface
-
5. Hygienic design
5.1 Cleaning
- Ideal cleaning for the shaft seals as these are fully integrated in the cleaning flow
5.2 Static seals
- Hygienic ring-shaped seal – no cavities
- FDA-approved elastometers in various qualities
5.3 Finished surface for parts coming into contact with product
- Electropolished for an ideal cleaning (Ra <0,8)
- Optional: Ra <0,4
5.4 Pump outlet/pump inlet
- Horizontal outlet for comprehensive draining
-
7. Corrosion free pump
7.1 Bearing bracket
- Design in stainless steel with high-performance bearing
7.2 Gearbox housing
- Aluminium design with a wear resistant and acid resistant Teflon coating
- Optional: Stainless steel design
-
2. Shaft seal
Same installation space for:
- Simple-acting slip-ring seal
- Double-acting slip-ring seal (safe-to-run dry with rinsing)
- Lip seal in cartridge design (safe-to-run dry without rinsing)
-
4. Pump housing
- Wear resistant Jung chrome carbide coating
- Optional: kolsterised finished surfaces
- Optional: Heating jacket
-
6. Easy to service design
6.1 Synchronisation gear wheels
- Inspection opening with access to the gearbox
- Setting the flank clearance in the system is possible without draining off the gearbox oil
6.2 Positioning
- Accurate positioning of the components due to precise production
6.3 Four guide bolts with capped nuts
- Quicker assembly/dismantling for inspection, servicing and/or manual cleaning
- Guide bolts for damage-free handling of the components
-
Advantages at a glance
- Considerable cost savings
Reduced investment and maintenance costs - Best quality
Made completely of stainless steel - Exceptional service-friendliness
The pump must not be removed from the plant for maintenance work - Utmost flexibility
A wide range of products, viscosities, and quantities can be handled with a single pump - Pumping is gentle and smooth
Low speed, minimum pulsation, no pressure surges - Highest hygiene level
No dead spaces, and particularly good flushing of the shaft seal - CIP and SIP
Cleaning and sterilisation within the plant, use as CIP feed pump
- Considerable cost savings
-
Technical data/Performance features
Downloads
Let's stay in touch!
Contact us