Digital twin – modelling the installation
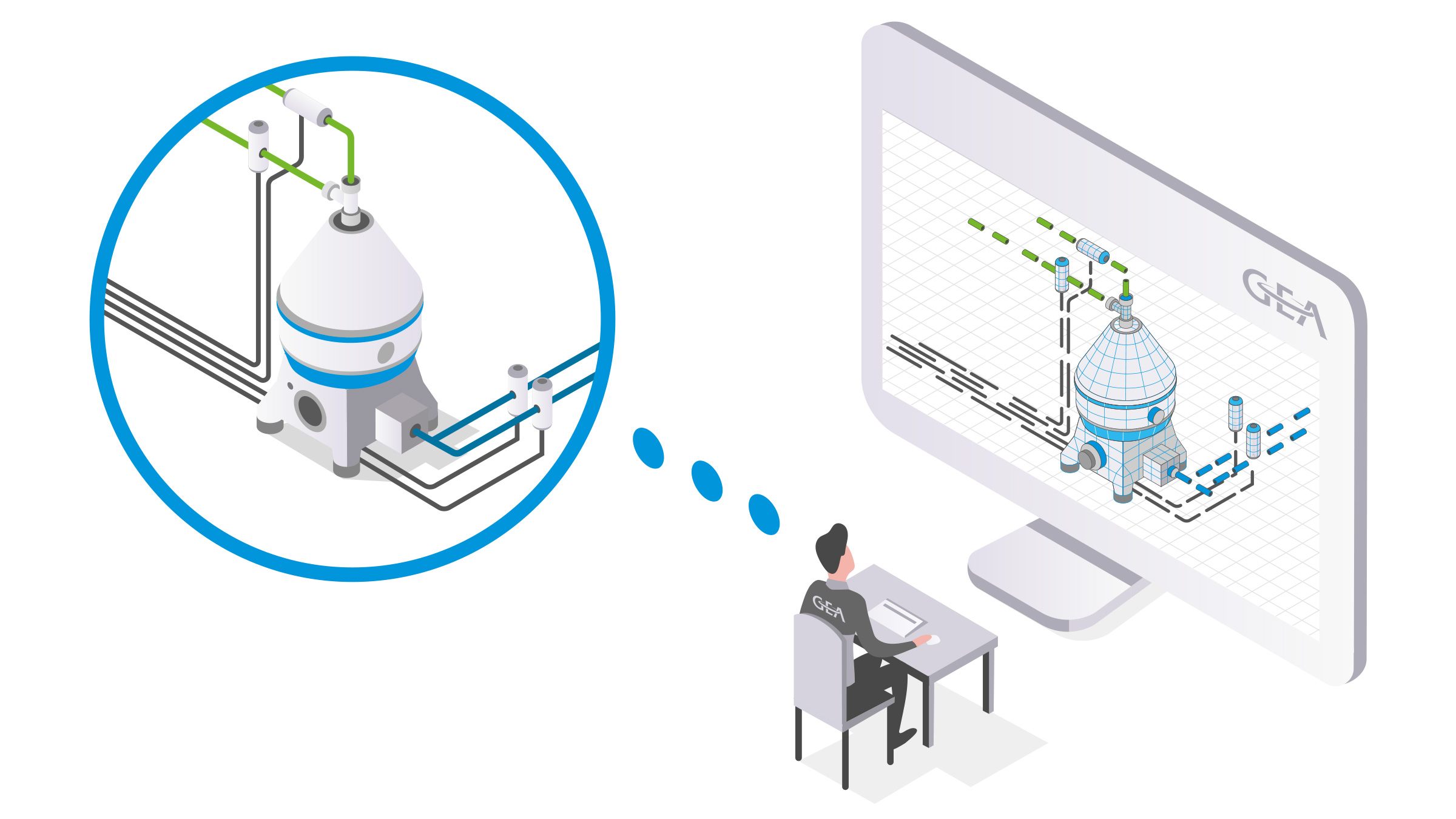
GEA has established a centrifuge simulation tool for software tests already in the development phase as well as during FAT (Factory Acceptance Test) and for virtual commissioning.
In doing so, the tool creates a digital twin of your installation. This simulation model is an image of the centrifuge and the complete subsequent installation and shows dynamic behavior while I/O simulation and fieldbus emulation.
During FAT the software can be tested independently from the centrifuge’s actual availability. Hence, potential software failures can be detected and solved much earlier resulting in better project execution and lower risks for our customers.
In doing so, the tool creates a digital twin of your installation. This simulation model is an image of the centrifuge and the complete subsequent installation and shows dynamic behavior while I/O simulation and fieldbus emulation.
During FAT the software can be tested independently from the centrifuge’s actual availability. Hence, potential software failures can be detected and solved much earlier resulting in better project execution and lower risks for our customers.
Virtual commissioning
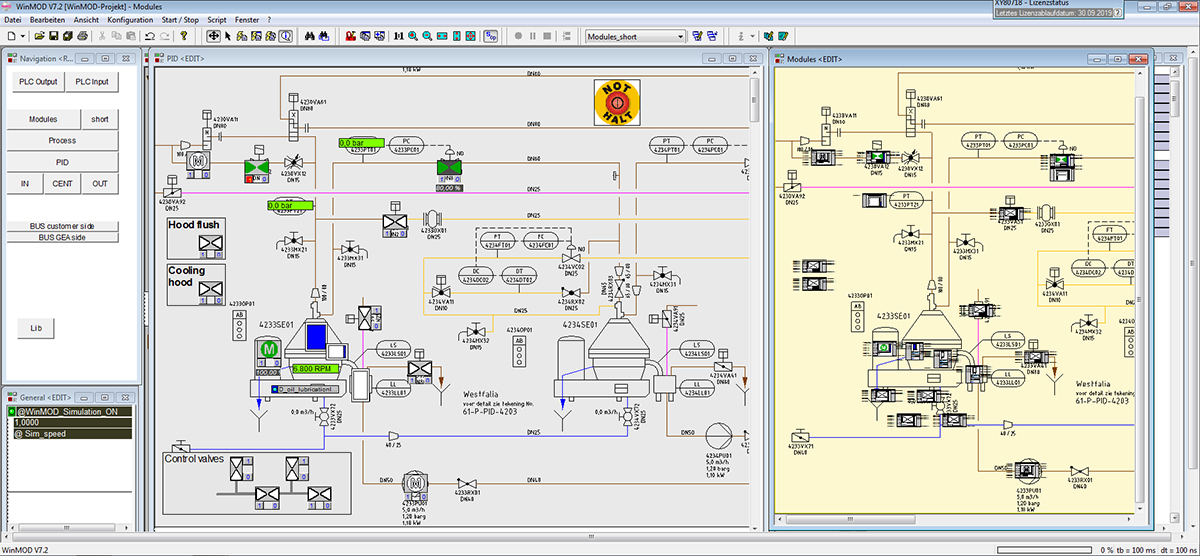
The virtual commissioning of the centrifuge ensures an early optimization of the software and ends up in a short commissioning time and fast production startup.
The benefits of our virtual commissioning according to VDI / VDE 3693 are
- Eliminated errors in the control code early on
- Tested and validated user interface
- Tested and validated sequences (e.g. ejection, CIP)
- Validated dynamic system behavior (e.g. reaction to turbidity changes in feed line)
- Tested unforeseen operating conditions
- Validated system parameters
- Simulated error scenarios
Let's stay in touch!
Learn more about innovations and our products, by signing up to our newsletter.
Contact us
We are here to help! With just a few details we will be able to respond to your inquiry.